This changes everything
The latest technology at your service in a practical and reliable way
How does it work?
Concrete Watcher™ uses a high-resolution camera to obtain video recordings from the interior of the drum. We record the entire loading, transport, and pouring process.
An Artificial Intelligence (A.I.) system analyzes and evaluates the recordings to determine slump, drum rotation, etc., and detect water additions in real time, among others.
The intelligent system saves the videos and produces reports in real time that can be consulted from anywhere, at any time.
Eliminate blind spots
Monitor the entire transport and delivery process: from the plant to the construction site, and back.
Store and analyze
Analyze and save records of each delivery to ensure complete traceability.
Automatic alerts
With compelling evidence of tampering or unauthorized additions, regardless of their origin.
Regulations and requirements
Meets project requirements requiring automatic slump and water additions control.
Greater benefits
Learn more about the delivery process and behavior of your concrete. Greater customer satisfaction.
Avoid cheating
Avoids quality problems by detecting if there is washing water left in the drum before loading a new batch.
360º control
Controls the behavior and performance of the concrete and the driver.
Real-time data and analysis
The Artificial Intelligence engine constantly monitors the interior of the drum. Analyzes and reports in real time.
Connectivity
It can be connected to automatic dosing equipment to add admixtures and/or water.
Learn about the benefits of Concrete Watcher™
Concrete Watcher™ provides numerous advantages to concrete producers and their customers, all of them with a high impact on performance and profits, while also avoiding traditional costs in the sector.
Quality improvements
- Detects water additions of any origin, thus preventing unauthorized additions.
- Detects the presence of water inside the drum before loading.
- Reduction of costs and carbon footprint by optimizing mix designs, without the need to overdesign to compensate for unauthorized water additions.
- Reduces the Cost of Low Quality, avoiding rejections on site due to incorrect mixing or workability.
- Ensures correct mixing, being able to detect clumps of dry material in the mix. It also helps with correct retempering if water and/or admixtures are added on site.
- It allows you to better understand the behavior of your concrete in transport: loss of workability over time, effect of adding water and/or admixtures, etc. This allows for a more optimized mix design for each situation.
- Reduces the need for on-site testing, reducing time and costs for the producer and the clients.
Logistics improvements
- Know in real time the volume of concrete poured and remaining inside the truck, optimizing the plant loading sequence (avoids idle time on site and delays in supply).
- Save pouring time by ensuring that the concrete arrives with the correct slump.
- Detects involuntary spills during transport. Connecting with the GPS system allows you to know exactly where they happened.
- Estimates the volume of concrete returned in case of partial discharge.
Other advantages
- Helps detect maintenance problems of the drum: blade wear, accumulation of hardened concrete, etc.
- Immediate alert if camera is blocked, helps with maintenance and avoids cheating on the system.
- Other alerts available: addition of water, slump out of specs, incomplete mixing, etc.
- Very simple installation, without connecting to any truck system (hydraulic, pneumatic, control unit). The installation can be carried out by any mechanic, both in the plant or at the shop.
- 100% contactless system: no consumables or wear for components.
Clear and precise information
It includes a complete management app, which analyzes and reports the events of each truck, on each trip. Designed to present information in a very clear and simple way. Always with relevant and updated information.
Truck chronology and incidents per trip
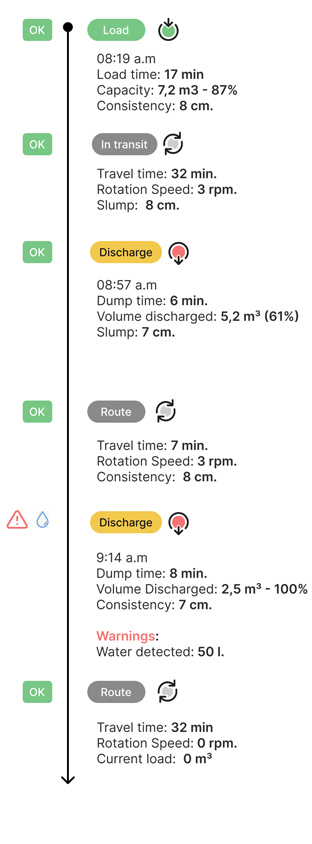
Views of incidents captured by video and analyzed by AI
concrete SPILLAGE
Alert detected: Spillage during transport! (0:15)
TRUCK ON SITE

Talk to a Concrete Watcher™ expert
CONCRETE WATCHER™ allows concrete producers to gain complete control over everything that occurs during transportation, being able to identify, analyze, and guarantee the quality of concrete from loading in the plant until complete discharge on site.
Parameters monitored by Concrete Watcher™
Slump and workability of concrete inside the truck
Alert for sudden changes in slump, e.g. when admixtures are added.
Pouring start time, total pouring time, volume poured and remaining in the truck, etc.
Detects water additions and estimates the total amount.
Direction and speed of rotation of the drum, total revolutions, mixing control.
Return concrete and/or washing water in the drum after completing the discharge
Installation and maintenance
The Concrete Watcher™ system has a very simple “plug and play” installation.
Click on the elements of the truck to see more information about the features.
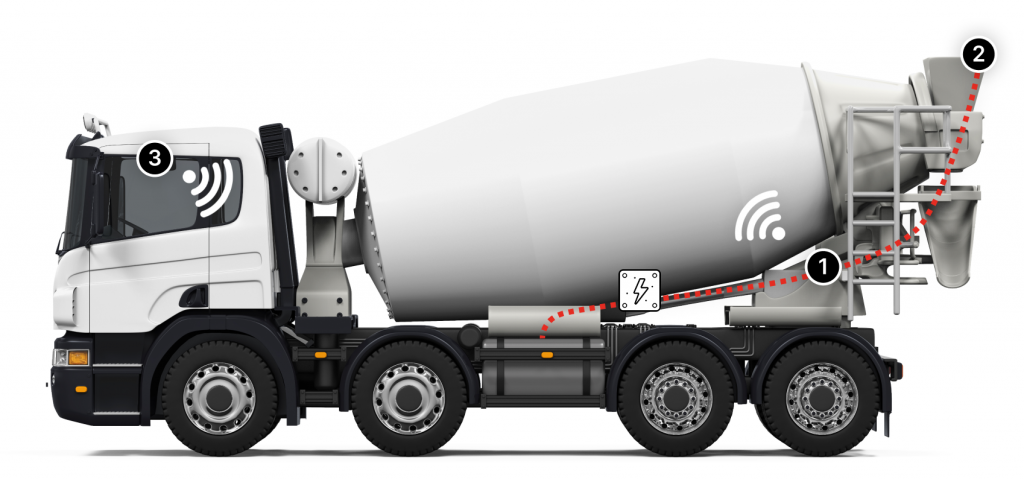
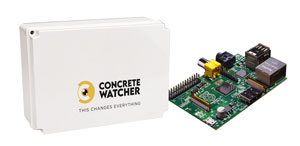
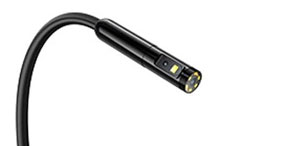
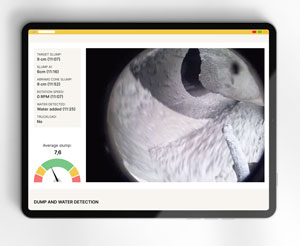
Solo necesita un poco de potencia de la caja de baterías externa (150W máx.)